Introduction and maintenance of concrete batching plant comp
Aggregate Bin of stationary concrete batching plant:
The aggregate bin is an important component of the whole concrete batching plant. It is mainly used to store aggregates, accurately meter and supply aggregates in time. Usually, the storage capacity of concrete batching plant is 1.25-2.5 times of the rated production capacity of the mixing equipment; the belt conveyor feeds in time to ensure the continuous operation of the concrete batching plant.
Check whether the door opening limit device is loose to avoid affecting the accuracy of drop value; check whether the vibration motor bolt is loose and the silo screen is blocked; check whether each roller has the situation of jam/non-rotation; check whether the belt is deviation, ect.
Belt conveyor of stationary concrete batching plant
The belt conveyor of aggregate conveying is a conveying equipment of batching plant with large conveying capacity, low operating cost and continuous conveying; it is suitable for conveying ordinary materials with loose density of 500~2500kg/m3; its working environment temperature is -10°C~40°C. In addition, the aggregate conveyors that work in special environment such as heat, cold, corrosion and other conditions, should take some appropriate protective measures to protect them.
Belt conveyor of conveying aggregate of stationary concrete batching plant:
Check whether there is any jam/non-rotation of each roller, the belt is deflected, or the bolts of each component are loose; check if the reducer has abnormal noise or oil leakage; check if the V-belt is slippery or loose.
After 100 working hours, apply grease to the tensioning screw of the belt conveyor; after 500 working hours, inspect the belt conveyor of batching plant.
Dust removal system of stationary concrete batching plant:
Dedusting of concrete batching plant is particularly important, cause the accumulation of dust brings inconvenience to the maintenance and repair of concrete batching plant, which degrades the performance of equipment and shortens the service life. Therefore, the dust removal system needs to be cleaned and maintained regularly.
Check the water collection condition of the air filter; clean the dust collector and the powder scale connection pipe, the connection pipe between the mixing machine and the dust collector; check and clean the filter element every month, and replace it timely if there's damage.
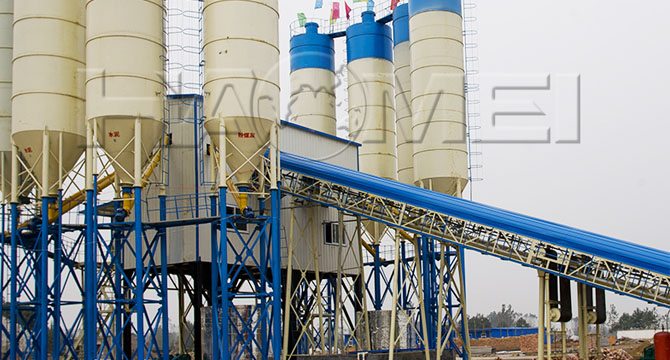
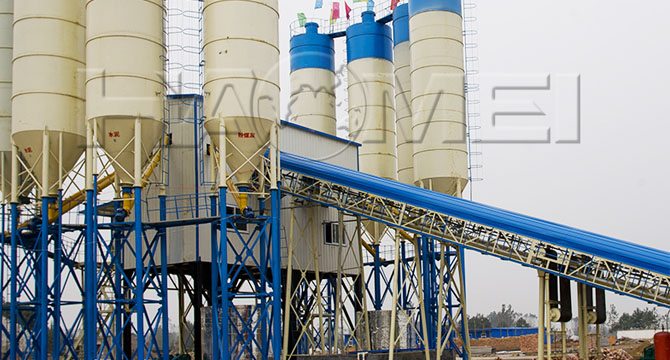
Mixing system of stationary concrete batching plant:
The mixing system is the core part of the concrete batching plant, and its working performance affects the production efficiency and quality of the concrete directly, so correct and regular maintenance is extremely important for batching plant's mixing system.
Each working group should clean the mixing shaft and mixing blades, rinse the bonding material in the mixing tank thoroughly.
The gap between the mixing blade and the lining plate should be adjusted frequently to prolong the service life of mixing blade and lining plate.
The mixing gearbox of the main engine should pay attention to refueling and oil change. When the mixing engine of batching plant is stopped, the oil level should be in the neutral position, that is, the red line position. The new machine should change oil after working 200 hours, after that, it can be replaced every 1500 hours.
Check whether the gear unit is running smoothly, has noise or abnormal noise. If the refueling/venting port can't breathe, it will result in oil leakage in the gearbox.
Check the belt of the mixing host. The belt should be free from cracks. It should be tightened, not slack.
Air compressor of stationary concrete batching plant:
The oil level in the crankcase of the air compressor should be above the minimum oil level marking line. Check the oil level and lubricating oil quality every 15 days or periodically. In addition, the air compressor of concrete batching plant should be placed in a flat, clean place and should not be placed in wet, dirty and dusty places.
Pull the thick oil pump twice every working day to supply oil to the shaft end seal; clean the air compressor filter once a week; check the sensitivity of safety valve every 3 months; clean the silencer every 250 hours; change the lubricant after working 500 hours.